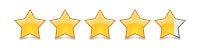
Operating system: Windows, Android, macOS
Group of programs: Business automation
System of technical maintenance and repair equipment
- Copyright protects the unique methods of business automation that are used in our programs.
Copyright - We are a verified software publisher. This is displayed in the operating system when running our programs and demo-versions.
Verified publisher - We work with organizations around the world from small businesses to large ones. Our company is included in the international register of companies and has an electronic trust mark.
Sign of trust
Quick transition.
What do you want to do now?
If you want to get acquainted with the program, the fastest way is to first watch the full video, and then download the free demo version and work with it yourself. If necessary, request a presentation from technical support or read the instructions.
Contact us here
How to buy the program?
View a screenshot of the program
Watch a video about the program
Download demo version
Compare configurations of the program
Calculate the cost of software
Calculate the cost of the cloud if you need a cloud server
Who is the developer?
Program screenshot
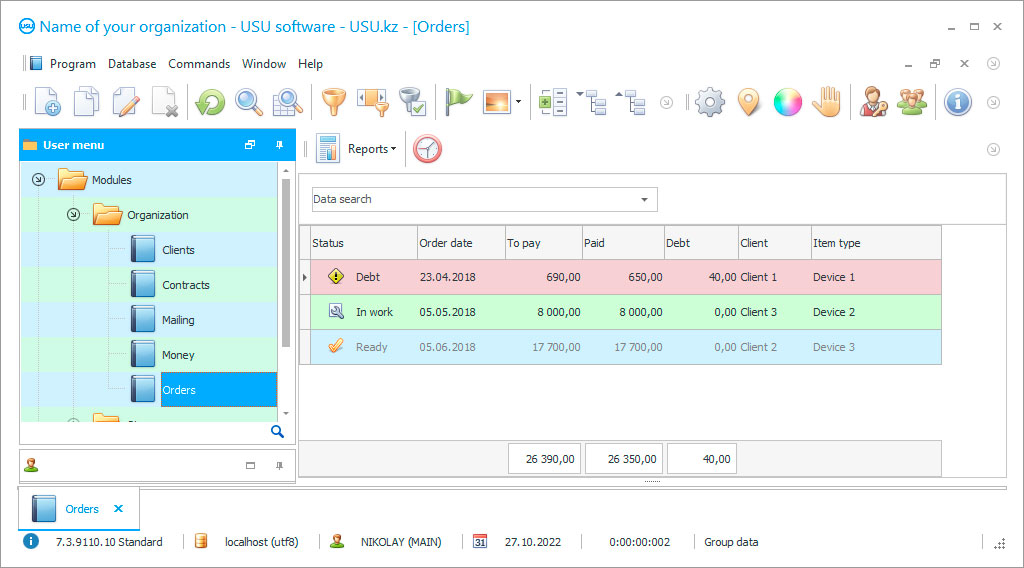
The system of equipment maintenance and repair is a set of organizational and technical measures taken by the enterprise management to the effective maintenance and repair of equipment. In addition to other tasks described in the interpretation of such a system, it includes the correct organization of inspection and repair of equipment, the ability to carry out repair work according to a schedule previously planned by the management, availability of the necessary stock or preliminary procurement of the necessary components. In general, the technical maintenance and repair system is due to a combination of regular maintenance between repair, as well as routine and overhaul repair that arise due to malfunctions in the technical condition of the equipment. To competently and effectively plan the actions of the repair crews, as well as to provide the equipment with a proper, and most importantly, regular inspection, it is imperative to introduce a special automated system in the management of the technical department, which provides a clear systematization and high-quality control over all processes in repair and maintenance. Are the managers of such enterprises facing a rather difficult task? Choose the most suitable functionality of a computer automation system from a variety of programs on the market.
The system installation, which has caused only unequivocally positive feedback from customers and has been in demand for many years, is presented by USU Software and is called the USU Software system. This unique program provides a multifunctional approach to the system of equipment maintenance and provides complete control at every stage of this repair activity, optimizing and organizing the work of personnel, saving them time. An automated application has a long list of advantages, but one of the most significant is its versatility and simplicity. The interface of the computer system is very easy and convenient to master on your own, so the management does not have to spend the budget to staff training or look for new staff. It is universal to the reason that it is able not only to keep records of personnel and processes of repair equipment services but also to take into account the tax, warehouse, and financial aspects of the enterprise. Plus, the vast majority of products and technical services are suitable for accounting in a system installation, even if you are dealing with semi-finished equipment products and component parts. In most trade and warehouse organizations, automation with the USU Software system is achieved by using and replacing personnel with special trade and warehouse equipment, with which the application easily interface. For example, employees often use a barcode scanner, a data collection terminal, and a label printer to identify technical goods, move them, write off or sell them, and many other devices are used in equipment trade.
Who is the developer?
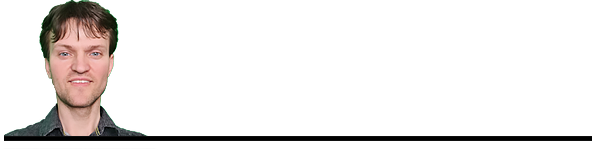
Akulov Nikolay
Expert and chief programmer who participated in the design and development of this software.
2024-05-18
Video of system of technical maintenance and repair equipment
This video can be viewed with subtitles in your own language.
If we still talk specifically about the system of maintenance and repair of equipment, then the universal technical maintenance system offers many organizing effective activities tools in this area. First of all, it is competent planning and operational tracking of the execution of applications. To ensure this, special nomenclature records are created in one of the sections of the main menu, which can be used both for registering and storing information about each task and identifying data on stocks of components and parts. Accepted applications are recorded in the records and fix such details as the date of submission and acceptance, the essence of the problem, location, the person who reported the problem, repair team, the execution deadline, and other parameters, according to the regulations of each enterprise. Records and all information contained in them can be cataloged and sorted in any order convenient for employees. Team leaders can mark themselves, or choose a responsible employee who oversees the processing of data. The status of execution of particular technical maintenance and repair tasks can be marked both with a text message and with a special clarity color. As for the timing, thanks to the functionality of the system installation, this parameter can be driven into the ‘Directories’ section and its observance become automatic, i.e. the program notifies the required staff when the deadline is coming to an end. The same goes for planning. By using the option of the USU Software system of the built-in scheduler, in which you can not only schedule and delegate the near future tasks, but also indicate the participants in the process, send them internal messages with details, notify them in advance, remind, and then, possibly, track their quality activities and timing of each request. Notes can be corrected and deleted as needed. The same method is convenient in parts accounting and components required for equipment maintenance. Indeed, to each of them it possible to describe and save its technical characteristics, as well as register its movement or write-off, if used during repairs. Plus, for each item, you can make and save a photo using a web camera. In addition to controlling the consumption of repairs parts and components, it is necessary to carry out their purchase, which must be properly planned. The toolkit of the ‘Reports’ section help the management and foremen with this, which is able to analyze the existing data in the database about what costs the enterprise incurs during planned overhauls of equipment and its maintenance, as well as to deduce the minimum stock rate that is necessary for the organization's activities in the conditions abnormal situation.
All of the above suggests that the implementation of the USU Software system is the best solution to all the tasks required for effective maintenance, as well as high-quality and timely equipment repair. We recommend that you follow the link posted on the official website of the USU Software, where you can easily download a free version of the software with limited functionality, to get to know this IT product in practice.
Download demo version
When starting the program, you can select the language.
Who is the translator?
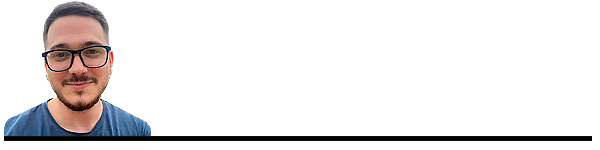
Khoilo Roman
Chief programmer who took part in the translation of this software into different languages.
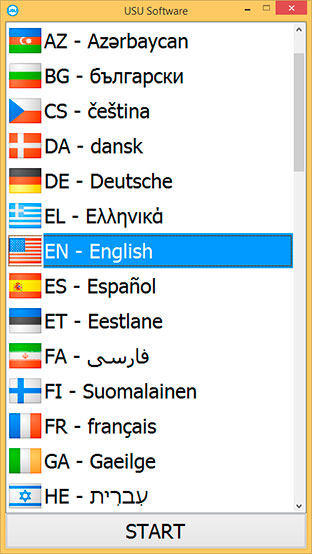
The USU Software system has many working with equipment built-in functions, periodically fixing its technical condition, maintenance, and decommissioning.
Essential equipment is also tracked in a special system to make it easier to track its needs and total inventory. Maintenance parameters are entered in separate structured tables that make up the ‘Modules’ section. General information about technical devices, their maintenance, and repair kept in different languages, thanks to the functions of the language interface pack.
Order a system of technical maintenance and repair equipment
To buy the program, just call or write to us. Our specialists will agree with you on the appropriate software configuration, prepare a contract and an invoice for payment.
How to buy the program?
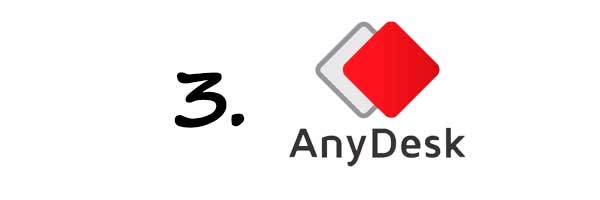
The program will be installed
If the program is purchased for 1 user, it will take no more than 1 hourBuy a ready-made program
Also you can order custom software development
If you have special software requirements, order custom development. Then you won’t have to adapt to the program, but the program will be adjusted to your business processes!
System of technical maintenance and repair equipment
The system workspace is divided into three most important categories: ‘References’, ‘Reports’, and ‘Modules’.
Section capabilities ‘Modules’ are able to automatically process and analyze a large amount of information in any direction. A smart system from the USU Software is capable of replacing a person in many daily work accounting activities operations, thanks to computerization. Management activities will be optimized as much as possible due to the possibility of continuous monitoring of current affairs online, as well as automatic generation of production reporting. Any internal documents of the organization can be created by the system mechanically, which undoubtedly speeds up work processes. The presence of archiving documents and general information in the program allows having permanent access to them and minimizing the likelihood of their loss. The backup option, where a copy can be saved to an external drive or even to the cloud, helps to ensure full control over current and past applications, as well as the safety of the information base. The multitasking and customizable interface makes work easier and makes accounting convenient.
To implement the function of automated formation of document flow, you need to take care of the availability of special user documentation templates. The success and timeliness of the execution of technical tasks can be viewed both in the context of departments and in the context of employees. With the use of the universal technical system, piecework payroll and its calculations become convenient and transparent.